Crankcase Relief Valve
Engine safety is critical in any application where high-powered internal combustion engines are used, from marine vessels to industrial machinery and power plants. These engines operate under intense conditions, with high temperatures, pressures, and the constant risk of internal component stress. To maintain safe, reliable engine performance, engineers have developed various protective mechanisms to prevent catastrophic failures—and among these, the crankcase relief valve stands out as an essential component.
The crankcase relief valve (CERV) is specifically designed to prevent dangerous pressure buildup within the engine’s crankcase. When engines operate under normal conditions, the CERV remains closed, helping to seal the crankcase and maintain balanced pressure. However, in the event of a crankcase explosion, such as from fuel vapor ignition, this valve opens, allowing excess pressure to escape safely. This release not only prevents serious damage to the engine but also protects operators and surrounding equipment from potentially dangerous blasts or fires.
This post will cover the main functions and components of a crankcase relief valve, explain how it works, and discuss why its presence is vital for engine longevity and operational safety. By understanding the importance of the crankcase relief valve, you’ll gain insight into how this device contributes to safer, more resilient engine systems, underscoring why it’s a standard feature in modern internal combustion engines.
What Are Crankcase Relief Valves?
A crankcase relief valve (CERV) is a vital safety component designed to protect internal combustion engines from dangerous pressure buildup within the crankcase. It serves as a pressure relief mechanism, opening when internal pressure exceeds a safe threshold, thus preventing catastrophic engine failures such as seizures, ruptures, or explosions. By venting excessive pressure, the valve ensures the engine operates safely under high-stress conditions.
Crankcase relief valves are typically used in environments where engines operate under extreme conditions, such as high temperatures and pressures. These conditions can create “hot spots” within the crankcase—localized areas where combustion gases accumulate and cause the internal temperature to spike. Hot spots can ignite fuel vapors, leading to dangerous explosions. Without a functioning crankcase relief valve, this pressure buildup and ignition risk can result in severe damage to engine components, including the crankcase rupture, engine seizure, and even fires.
CERVs are especially crucial in industrial settings such as marine vessels, power plants, and heavy machinery, where large, high-powered engines are constantly exposed to extreme conditions. These valves are also important in high-performance automotive engines, where the risk of pressure surges and hot spots is heightened. By releasing excess pressure and preventing flame propagation, the crankcase relief valve mitigates the risks posed by hot spots, protecting both the engine and surrounding infrastructure, and ensuring safe, reliable operations.
Main Components of a Crankcase Relief Valve
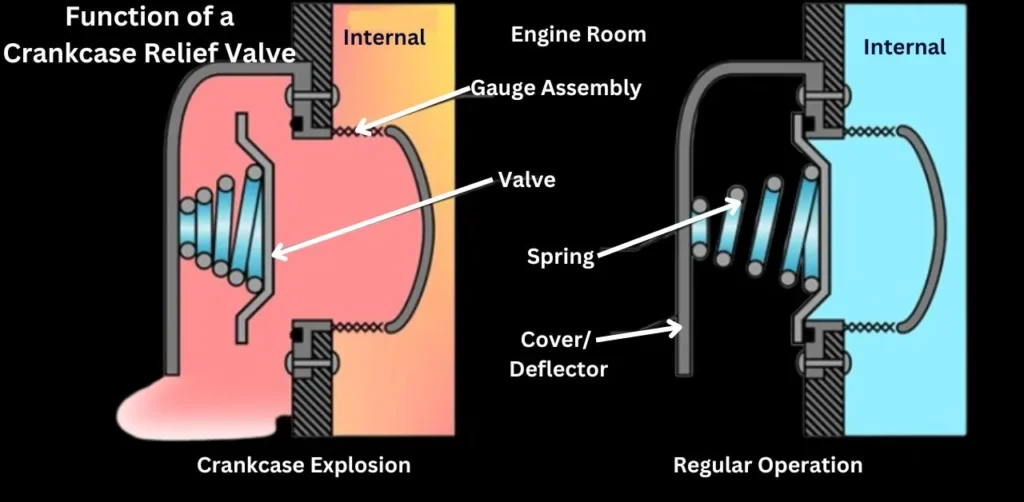
A crankcase relief valve (CERV) is designed with several key components that work together to manage internal pressure and prevent damage from crankcase explosions. Each component plays a specific role in the safety and functionality of the valve.
- Gauge Assembly / Fire Arrester: The gauge assembly includes a fire arrester, which is essential for preventing flames from escaping the crankcase. In the event of combustion within the crankcase, the fire arrester cools and disrupts the flame front, ensuring that any flames are contained and do not ignite surrounding flammable materials.
- Valve: The main valve is the central part of the crankcase relief system. It remains closed during normal operation, forming a seal that maintains stable crankcase pressure. When excessive pressure builds up, the valve opens to provide a safe passage for gases to escape.
- Spring: The spring mechanism holds the valve in a closed position under normal conditions. It is calibrated to open only when crankcase pressure reaches a critical threshold, ensuring that the valve operates only when necessary to release excess pressure.
- Cover Deflector: The cover deflector directs escaping gases away from the engine and surrounding areas when the valve opens. It prevents these gases from causing damage to nearby components and helps maintain a safer environment around the engine by containing the release path.
Each component of a crankcase relief valve is essential for its safe operation, preventing dangerous over-pressurization and containing potential combustion within the crankcase.
Function of a Crankcase Relief Valve
A crankcase relief valve (CERV) is essential for maintaining safe pressure levels within an engine’s crankcase, particularly under extreme conditions.
- Normal Operation: During standard engine operation, crankcase relief valves remain closed, effectively sealing the crankcase and keeping the internal pressure within safe limits. This closed position is maintained by a spring force that holds the valve shut unless excessive pressure builds up.
- Response to Crankcase Explosion: In the event of a crankcase explosion, there’s a rapid increase in pressure within the crankcase. Without a pressure relief mechanism, this pressure can lead to severe outcomes, such as engine seizure, component damage, or even crankcase rupture.
- How the Valve Works: When internal pressure spikes, it exerts force on the valve plate, overcoming the spring’s resistance and opening the valve. This creates an escape path for high-pressure gases, allowing them to vent from the crankcase and preventing over-pressurization that could lead to further damage.
- Flame Arrester Mechanism: To prevent flames from escaping and igniting nearby combustible materials, the valve includes a flame arrester. This component cools combustion gases and disrupts the flame front, containing flames within the valve to avoid external ignition risks.
- Returning to Closed Position: After the excess pressure is released, the spring mechanism re-closes the valve, restoring the crankcase to a sealed state and maintaining the engine’s standard operating pressure.
What Damage Is Caused Without a Crankcase Relief Valve?
A crankcase relief valve (CERV) is essential in maintaining the safety and integrity of an internal combustion engine by controlling internal pressure. Without a CERV, engines are vulnerable to several serious risks that can lead to significant damage, operational failure, and safety hazards. Below are the key risks associated with the lack of a crankcase relief valve:
1. Engine Component Damage
High internal pressure in the crankcase can cause severe damage to critical engine components. When the pressure is not regulated, it can force seals and gaskets to crack or deteriorate, allowing for leaks of gases or fluids. This pressure buildup can also weaken the engine’s structural integrity, potentially resulting in the bending or warping of vital parts, such as the crankshaft or cylinder block. Over time, this damage can lead to costly repairs or engine failure.
2. Explosion Hazards
One of the most dangerous risks of not having a crankcase relief valve is the potential for catastrophic failure and explosion. Excessive pressure in the crankcase can cause a rupture, leading to a violent explosion. This is especially hazardous in high-powered engines, such as those found in marine vessels, power plants, and heavy industrial machinery. A crankcase explosion can not only destroy the engine but also pose a significant risk to operator safety and nearby equipment.
3. Oil Contamination and Leakage
Uncontrolled pressure can force engine oil to leak out of its designated pathways, leading to oil contamination throughout the engine components. Oil leaks can lead to further damage, such as fouling of critical sensors or interference with lubrication systems. This contamination can also cause overheating and premature wear of engine parts. Additionally, excessive pressure can force oil past gaskets and seals, resulting in significant oil loss and operational inefficiency.
4. Real-World Examples
The absence of a crankcase relief valve has led to catastrophic incidents in various industries. For instance, in the maritime industry, there have been numerous cases of ship engines experiencing crankcase explosions due to uncontrolled pressure buildup, causing massive damage to engine rooms and even posing life-threatening risks to crew members. Similarly, in power plants, engines without proper pressure relief have resulted in extensive damage, downtime, and costly repairs, as well as potential environmental hazards from oil and fuel leakage.
Who Invented the Crankcase Explosion Relief Valve (CERV)?
Crankcase relief valves were developed in the 1950s by the British Internal Combustion Engine Research Association (BICERA), an organization formed in 1948 in response to a series of hazardous crankcase explosions on ships. Recognizing the need for improved safety in engine operations, BICERA conducted extensive research into the causes of these explosions and designed safety devices, including the crankcase relief valve.
In 1954, BICERA patented the first crankcase explosion relief valve. This pioneering valve was engineered to open and release internal pressure in the event of a crankcase explosion, protecting the engine from damage. Additionally, the valve included a mechanism to prevent flames from escaping the crankcase, mitigating the risk of secondary fires.
Today, crankcase explosion relief valves have become a standard safety feature on nearly all medium and large internal combustion engines, underscoring their importance in enhancing engine safety and preventing catastrophic failures.
FAQ on Crankcase Relief Valve
Q. What is a crankcase relief valve?
A. A crankcase relief valve opens to release pressure during a crankcase explosion and prevents flames from escaping the engine.
Q. How to check a crankcase relief valve?
A. You can check the valve using an air and methane mixture with a methane concentration of 9.5% ± 0.5%.
Q. What causes a crankcase explosion?
A. A crankcase explosion is caused by the ignition of oil mist inside the crankcase.
Q. How to prevent a crankcase explosion?
A. Crankcase explosions can be prevented by using oil mist detectors and spring-loaded relief valves that release pressure when it gets too high.
Conclusion
In summary, the crankcase relief valve (CERV) plays an indispensable role in safeguarding engines by controlling internal pressure and preventing catastrophic failures such as explosions or fires. By allowing pressure to safely escape in the event of a crankcase explosion, it helps protect vital engine components, ensuring the overall safety and reliability of the engine.
However, the effectiveness of the crankcase relief valve depends on regular maintenance and inspection. Over time, wear and tear can affect its performance, so routine checks are essential to ensure it operates as designed. Keeping the valve in good condition not only enhances engine safety but also minimizes the risk of costly repairs and downtime.
As technology continues to advance, so too does the design and functionality of crankcase relief valves. Innovations in materials, precision engineering, and automated monitoring systems are making these valves more efficient and reliable, further improving engine safety and operational efficiency. The ongoing improvements in CERV technology ensure that engines, especially high-powered industrial and automotive models, remain more secure and perform at their best for years to come.