In the demanding world of marine operations, ensuring the optimal performance of marine engines is crucial. Engine monitoring systems play a vital role in safeguarding engine health, reducing downtime, and maximizing efficiency. By providing real-time data and early warnings of potential issues, these systems significantly enhance safety and reliability, ensuring vessels operate smoothly even in challenging conditions.
In this blog we will discuss about the the five best engine monitoring systems tailored specifically for marine engines. From temperature sensors and water-in-oil detection to advanced solutions like MetaPower Quad, discover how these cutting-edge technologies keep marine engines running at their best.
1. Main Bearing Temperature Sensors
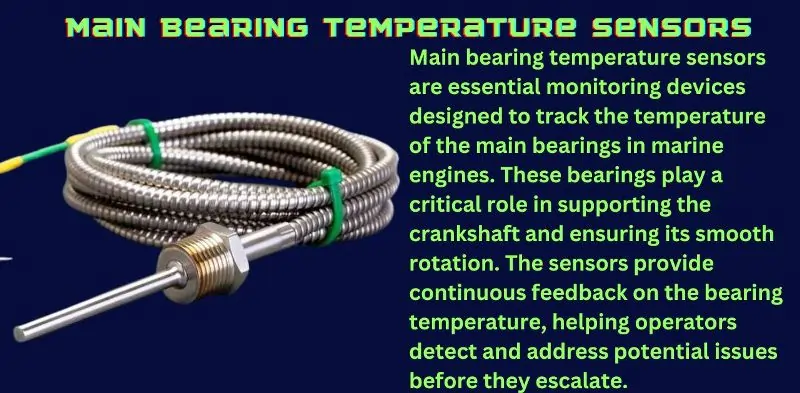
What They Are
Main bearing temperature sensors are essential monitoring devices designed to track the temperature of the main bearings in marine engines. These bearings are essential for providing support to the crankshaft and facilitating its seamless rotation.. The sensors provide continuous feedback on the bearing temperature, helping operators detect and address potential issues before they escalate.
Importance
- Early Detection of Overheating: Overheating in main bearings can lead to excessive wear, loss of lubrication, and, ultimately, bearing failure. Temperature sensors allow operators to spot abnormal temperature rises early and take corrective action.
- Ensures Smooth Operation: By maintaining optimal bearing conditions, these sensors protect critical engine components, reduce unplanned downtime, and extend the lifespan of the engine.
How They Work
- Placement in Main Bearings: Sensors are strategically installed within the engine’s main bearing assembly to monitor temperature directly at the source.
- Continuous Monitoring: These devices provide real-time temperature readings, which are integrated into the engine control system. If temperatures exceed safe operating thresholds, alarms are triggered to alert operators of the issue.
Example System
One leading example is the Kongsberg Main Bearing Temperature Sensor System, which offers high-precision temperature measurement and seamless integration with modern engine monitoring platforms. Its robust design ensures reliable operation in harsh marine environments, making it a trusted choice for ship operators worldwide.
Main bearing temperature sensors are an indispensable tool for maintaining marine engine health and preventing costly failures. Their precision and reliability make them a cornerstone of modern engine monitoring systems.
2. Cylinder Liner Temperature Sensor
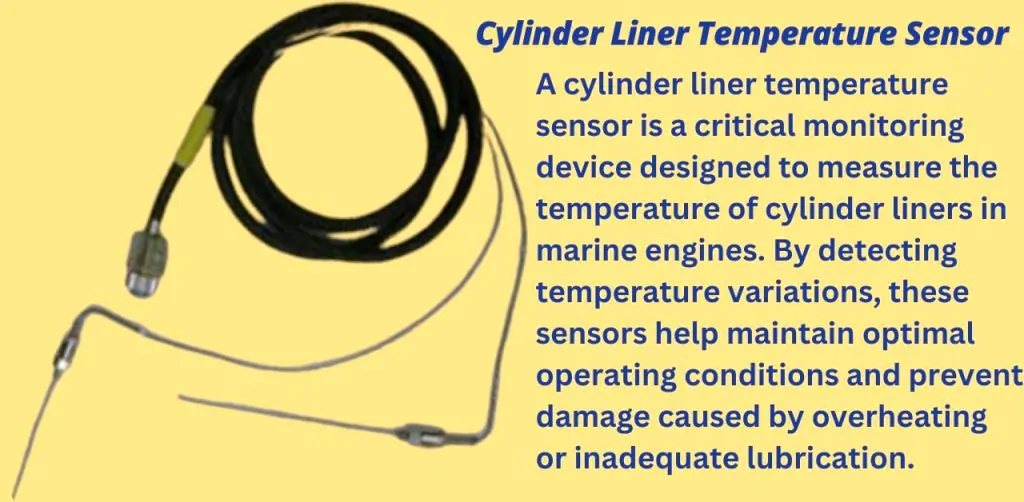
What It Is
A cylinder liner temperature sensor is a critical monitoring device designed to measure the temperature of cylinder liners in marine engines. By detecting temperature variations, these sensors help maintain optimal operating conditions and prevent damage caused by overheating or inadequate lubrication.
Importance
- Early Problem Detection: Abnormal cylinder liner temperatures can indicate issues such as insufficient cooling, lubrication problems, or combustion irregularities. Early detection helps prevent severe damage.
- Ensures Efficient Combustion: Maintaining the correct cylinder liner temperature is essential for efficient fuel combustion, which reduces fuel consumption and emissions.
- Prolongs Component Life: Regular monitoring of liner temperatures helps operators identify and address wear-related issues, extending the lifespan of critical engine components.
Key Features
- Real-Time Monitoring: Provides continuous temperature readings, enabling operators to react promptly to deviations from normal operating ranges.
- High Precision: Designed to operate in high-temperature environments, these sensors deliver accurate and reliable data even under extreme conditions.
- Alarm Integration: Many systems are equipped with alarms that trigger alerts when temperatures exceed safe thresholds, ensuring immediate action can be taken.
- Ease of Integration: Cylinder liner temperature sensors are often compatible with broader engine monitoring systems, providing a holistic view of engine health.
How It Works
The sensor is installed directly in or near the cylinder liner to capture temperature readings at critical points. The data collected is transmitted to the engine control system, where it is analyzed for abnormalities.
Example System
The MAN Cylinder Liner Temperature Sensor is a notable example, offering advanced temperature monitoring for large marine engines. This sensor delivers high accuracy and integrates seamlessly with engine management systems to enhance operational safety and efficiency.
Conclusion
Cylinder liner temperature sensors are indispensable for modern marine engine management, ensuring efficiency, reliability, and longevity. By providing real-time insights and early warning of potential issues, these sensors play a pivotal role in keeping engines running smoothly and avoiding costly repairs
3. Crosshead and Crank Temperature Monitoring
Significance of Monitoring Crosshead and Crank Temperatures
Monitoring the temperatures of crosshead and crank components in an engine is critical for maintaining operational efficiency and ensuring the longevity of the machinery. This practice offers the following key benefits:
- Avoiding Catastrophic Failures: Abnormal temperature fluctuations often indicate potential issues such as improper lubrication, excessive wear, or misalignment. Early detection helps in preventing severe damage to engine components and costly downtime.
- Prolonging Engine Component Life: Consistent monitoring ensures optimal operating conditions, reducing unnecessary strain and wear on the engine’s critical components. This results in improved reliability and longer service intervals.
Features of Modern Temperature Monitoring Systems
Modern crosshead and crank temperature monitoring systems come equipped with advanced features designed to enhance efficiency and safety:
- Real-Time Data Logging: Continuous temperature measurement allows operators to track performance trends over time. This data helps in predictive maintenance and informed decision-making.
- Integration with Alarms and Automatic Shut-Off Systems: These systems are programmed to trigger alarms or initiate shutdown procedures if temperatures exceed preset thresholds, preventing escalation of issues.
- User-Friendly Interfaces: Intuitive displays and remote accessibility enable seamless monitoring and troubleshooting.
- Robust Sensors: High-precision sensors ensure accurate readings even under extreme conditions, enhancing reliability.
Practical Applications
Real-world applications highlight the effectiveness of temperature monitoring systems:
- Case Study 1: Preventing Bearing Failure A vessel equipped with a real-time monitoring system detected a gradual temperature rise in the crank bearing. Upon investigation, it was found that the lubrication flow was partially obstructed. Prompt action prevented a bearing failure, avoiding expensive repairs and operational delays.
- Case Study 2: Improving Maintenance Efficiency An engine maintenance team used historical temperature data to identify wear patterns in crosshead components. This allowed for targeted maintenance, reducing the frequency and cost of unplanned overhauls.
- Case Study 3: Alarm Integration Saving the Day During a long-haul voyage, an automatic shut-off system was triggered due to a sudden temperature spike in the crosshead area, caused by an oil pump malfunction. The quick response prevented severe engine damage, showcasing the importance of system automation.
4. MetaPower Quad: Advanced Monitoring Solution
Introduction to MetaPower Quad
The MetaPower Quad is an innovative monitoring solution designed to meet the demanding requirements of modern industrial and marine engines. With its advanced capabilities, this system provides unparalleled insights into engine performance and health, enabling operators to maintain optimal efficiency and reliability.
Features and Benefits
Multi-Point Data Collection for Comprehensive Insights
The MetaPower Quad excels in gathering data from multiple critical points within the engine. This comprehensive approach ensures:
- Accurate Monitoring: Real-time measurements of key parameters such as temperature, pressure, and vibration.
- Holistic Analysis: Integrated data provides a complete picture of engine performance, helping identify inefficiencies or potential failures.
Enhanced Diagnostics for Predictive Maintenance
With its cutting-edge diagnostic tools, the MetaPower Quad enables:
- Early Fault Detection: Advanced algorithms analyze trends to detect anomalies before they escalate.
- Reduced Downtime: Predictive insights allow for timely maintenance planning, minimizing unscheduled repairs.
- Cost Efficiency: Avoiding catastrophic failures translates to significant savings in repair and replacement costs.
Why It Stands Out
Comparison with Conventional Monitoring Systems
The MetaPower Quad outperforms traditional systems through its:
- Precision and Scope: While conventional systems monitor limited parameters, the MetaPower Quad’s multi-point data collection ensures a broader and more precise understanding of engine health.
- Automation and Integration: Equipped with smart automation, it integrates seamlessly with alarm and shutdown protocols, ensuring immediate response to critical conditions.
- User-Friendly Interface: Intuitive dashboards and remote accessibility simplify monitoring and troubleshooting.
Real-World Examples of Effectiveness in Marine Engines
- Case Study: Optimized Fuel Efficiency A shipping company equipped its fleet with MetaPower Quad systems, leading to a 15% improvement in fuel efficiency. Real-time monitoring helped optimize engine settings and reduce unnecessary fuel consumption.
- Case Study: Preventing Major Engine Failure The system detected abnormal vibration levels in a vessel’s crankshaft. Immediate action was taken, preventing a major failure that could have resulted in significant financial losses and operational delays.
- Case Study: Streamlined Maintenance Historical data collected by MetaPower Quad enabled engineers to identify wear patterns in engine components. This allowed the company to transition from reactive to proactive maintenance, reducing overall maintenance costs by 20%.
5. Water in Oil Sensors
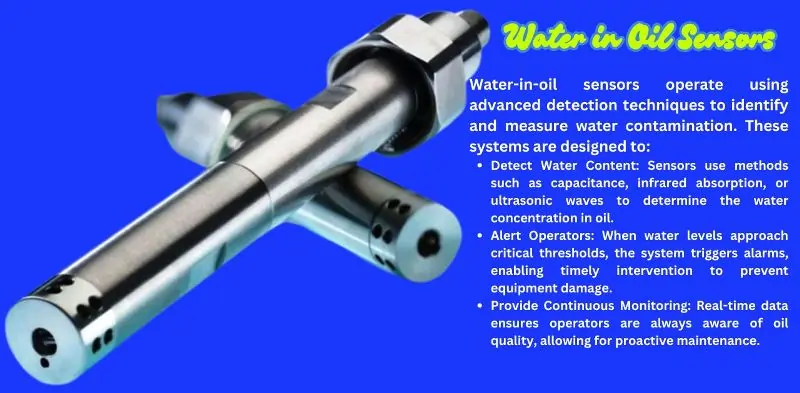
Why Monitor Water in Oil?
Monitoring water content in oil is essential for maintaining the efficiency and longevity of machinery. Key reasons for this include:
- Preventing Contamination-Related Wear and Corrosion: Water contamination can lead to the formation of rust and other corrosive by-products, damaging critical components. Additionally, it accelerates wear by compromising the protective film provided by the oil.
- Ensuring Proper Lubrication Performance: Excess water in oil reduces its viscosity and compromises its lubricating properties, leading to increased friction, overheating, and potential mechanical failures.
How It Works
Water-in-oil sensors operate using advanced detection techniques to identify and measure water contamination. These systems are designed to:
- Detect Water Content: Sensors use methods such as capacitance, infrared absorption, or ultrasonic waves to determine the water concentration in oil.
- Alert Operators: When water levels approach critical thresholds, the system triggers alarms, enabling timely intervention to prevent equipment damage.
- Provide Continuous Monitoring: Real-time data ensures operators are always aware of oil quality, allowing for proactive maintenance.
Market-Leading Examples
Reliable Products with Advanced Detection Capabilities
- SKF Oil Quality Sensor
- The SKF Oil Quality Sensor offers real-time monitoring of water content, oil degradation, and contamination levels. Its compact design and robust performance make it a popular choice for industrial and marine applications.
- Parker Kittiwake Water in Oil Sensor
- This sensor uses capacitive measurement technology to provide precise water content readings. With features like integrated alarms and compatibility with various oil types, it is a trusted solution for maintaining oil integrity.
- EESIFLO® Inline Water in Oil Monitor
- Renowned for its accuracy and durability, the EESIFLO sensor continuously measures water content in oil streams, ensuring immediate detection and action against contamination.
Conclusion
In conclusion, effective monitoring systems are essential for ensuring the reliability and longevity of marine engines. By providing real-time insights and enabling predictive maintenance, these systems help prevent costly breakdowns and optimize overall performance. Regular maintenance, combined with the right monitoring tools, is a proactive approach to safeguarding your investment and keeping your operations running smoothly.
Investing in advanced solutions like MetaPower Quad or water-in-oil sensors can make a significant difference in your engine’s health and efficiency. Don’t wait for problems to arise—take action today.
Explore these cutting-edge systems to ensure your marine engine operates at its best and remains a dependable asset for years to come.