Fusible Plugs
Fusible plugs are essential safety devices in marine applications, specifically engineered to prevent overheating in ship boilers and high-temperature equipment. On marine vessels, these plugs act as a critical fail-safe, automatically releasing pressure when temperatures exceed safe limits. This function is vital in preventing potential disasters like boiler explosions that could jeopardize crew safety and vessel integrity.
Marine equipment operates under demanding conditions, so reliable safety measures are crucial. Fusible plugs provide that additional layer of protection, making them indispensable for controlling heat and pressure on board. For 2025, updated safety guidelines for fusible plugs focus on advancements in materials, installation methods, and maintenance tailored to marine settings.
This guide will cover everything from the purpose and materials of fusible plugs to best installation practices, providing the most up-to-date safety information to keep your vessel compliant and safe in marine environments.
What Are Fusible Plugs?
Fusible plugs are critical safety devices designed to protect high-temperature, high-pressure systems from overheating. Used in equipment like pressure vessels, boilers, and compressed air systems, fusible plugs function by melting at a predetermined temperature, releasing pressure to prevent potential hazards like explosions. Their primary role is to serve as a fail-safe, releasing excess pressure when temperatures surpass safe operational levels.
Key Applications of Fusible Plugs
Fusible plugs are widely utilized across industries where controlling temperature is essential for safe equipment operation. They are commonly found in:
- Industrial Boilers: Especially in coal-fired boilers, where high temperatures pose a risk of overheating.
- Pressure Vessels: Used in vessels storing pressurized gases to release pressure if temperature limits are breached.
- Compressed Air Systems: Installed to prevent thermal damage from excessive heat buildup.
These applications rely on fusible plugs as a final safeguard against overheating, protecting both equipment and operators.
The Importance of Fusible Plugs for Safety
In high-temperature systems, maintaining safe operation is crucial, as excess heat can compromise equipment integrity and increase the risk of dangerous failures. Fusible plugs are indispensable in these environments, where they enhance safety by providing a straightforward, reliable response to extreme temperatures. By melting and relieving pressure before equipment reaches a critical point, fusible plugs help prevent catastrophic incidents, making them essential components in many industrial settings.
Fusible Plug Materials
Fusible plugs are made from materials chosen specifically for their low melting points, allowing them to respond quickly to high temperatures. Common materials include alloys like lead, tin, and bismuth, which melt at relatively low temperatures compared to the surrounding metal components. These materials are designed to activate at specific temperature thresholds, providing a reliable safety response to overheating in high-pressure systems.
How Material Choice Impacts Safety and Performance
The choice of fusible plug material is crucial, as it directly affects the device’s sensitivity and effectiveness. A material with too high a melting point might not activate in time to prevent damage, while a material with too low a melting point may trigger prematurely. By selecting alloys with precise melting temperatures, manufacturers ensure that fusible plugs operate safely within the intended range, activating only when truly necessary.
Why Certain Materials Are Better for Specific Temperature Ranges
Different industrial applications require fusible plugs that activate at specific temperature ranges, depending on the machinery and operational environment. For example:
- Lead alloys are often used in standard industrial applications due to their moderate melting points.
- Bismuth alloys are preferred in applications requiring higher melting temperatures, offering protection in more intense heat settings.
How Fusible Plugs Work
Fusible plugs are designed to prevent dangerous overheating in high-pressure systems by using a simple, self-actuating mechanism that responds automatically to excessive heat. Here’s a thorough breakdown of how they work:
- Temperature Monitoring: Fusible plugs contain a core made from a metal alloy with a specific melting point. This alloy is chosen to match the maximum safe operating temperature of the equipment, allowing the fusible plug to “sense” when temperatures exceed safe limits.
- Response to Overheating: When the equipment’s temperature rises and approaches the alloy’s melting point, the fusible plug begins to soften. As the temperature continues to increase, the alloy core fully melts, creating an open path for pressure release.
- Self-Actuating Release: Once the core melts, the fusible plug allows built-up pressure or steam to escape through the open pathway. This release prevents further temperature rise, stabilizing the system and protecting it from overheating.
- Accident Prevention: By releasing excess pressure automatically, fusible plugs prevent potential accidents such as explosions or structural damage to the equipment. Their self-actuating design ensures rapid response without requiring external controls or electrical components, making fusible plugs a reliable fail-safe in high-temperature applications.
Formulas and Calculations Related to Fusible Plugs
Melting Point Calculation
The following formula is used to find the melting point of the fusible substance used in a plug:
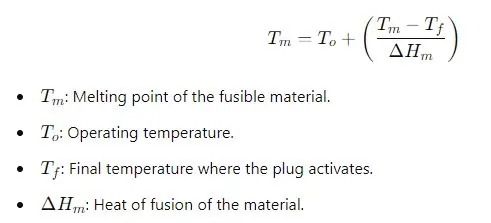
Pressure Relief Capacity
The pressure relief capacity of a fusible plug can be calculated using this formula:
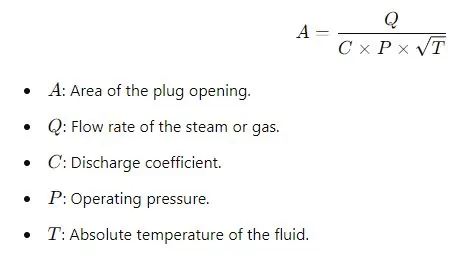
Time to Meltdown
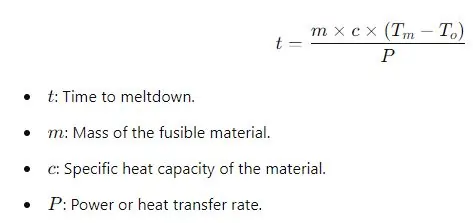
What Is the Purpose of a Fusible Plug?
Fusible plugs serve as an essential safety feature in high-temperature, high-pressure systems. Their primary purpose is to prevent dangerous pressure buildup and equipment failure by automatically responding to excessive heat. These plugs act as a fail-safe, ensuring that machinery remains safe and operational even in the event of system malfunction or temperature irregularities.
Preventing Pressure Buildup and Equipment Failure
In many industrial systems, such as boilers, pressure vessels, and steam systems, pressure and temperature must be closely controlled to prevent catastrophic failures. When a system begins to overheat, pressure increases, which can lead to equipment damage or even explosions. Fusible plugs help mitigate these risks by providing an automatic pressure release when temperatures exceed safe levels. By melting at a specific temperature, they release pressure and allow the system to stabilize before damage occurs.
Final Safety Measure Against Overheating
Fusible plugs act as a final line of defense in protecting critical equipment from overheating. While other safety mechanisms, like pressure relief valves, help manage overpressure, fusible plugs focus on temperature-related hazards. When all other systems fail to manage overheating, the fusible plug melts, activating a safety response and protecting both the equipment and the personnel from potential accidents.
Industry Regulations and Safety Standards
Industry regulations and safety standards require the use of fusible plugs in many applications to ensure safe operation. These standards dictate specific materials, installation practices, and maintenance schedules to ensure that fusible plugs perform reliably in preventing overheating. Compliance with these regulations is crucial for minimizing risks and ensuring the safe operation of equipment in industries such as manufacturing, marine, and power generation.
Where to Install a Fusible Plug in Marine Applications
In marine environments, fusible plugs are essential for protecting vessels’ critical systems, particularly in boilers and pressure vessels that handle high temperatures and pressures. Proper installation is key to ensuring these plugs function effectively in preventing accidents like explosions or equipment failure. Below are the optimal locations for installing fusible plugs on marine vessels:
Optimal Installation Locations
- Marine Boilers: Fusible plugs should be installed in the hottest areas of the boiler, typically in the firebox or near the superheater tubes. This ensures that the plug responds to excessive temperatures in the critical sections of the boiler, preventing overheating and catastrophic failures.
- Pressure Vessels: On vessels with pressure vessels (such as those storing pressurized gases or liquids), fusible plugs should be installed at the highest point of the vessel where heat and pressure are likely to accumulate. This placement allows the plug to act promptly in releasing pressure when temperatures exceed safe limits.
- Steam Systems: In steam systems aboard ships, fusible plugs should be installed near the steam drum, steam headers, or other key areas where temperature and pressure can spike. These plugs help protect the system from overheating and maintain the safety of the crew and vessel.
- Compressed Air Systems: Fusible plugs in air compressors should be installed in the air receiver or pressure chambers where excessive heat buildup could occur, especially when the system is under load.
Tips for Maximum Effectiveness
- Ensure plugs are installed in areas with consistent heat exposure to allow for timely activation.
- Use multiple plugs if necessary, especially in large systems, to provide comprehensive protection across different components.
- Regularly inspect and maintain fusible plugs to ensure they are free from debris or corrosion that could impair their function.
Hazards of Incorrect Installation
Incorrect installation of fusible plugs can result in delayed or failed activation, potentially leading to overheating, pressure buildup, and catastrophic damage to vital systems. Placing the plug in areas that are not prone to overheating or where heat distribution is uneven may render the device ineffective. Additionally, improper sealing or using the wrong type of plug for specific system pressures and temperatures can compromise safety. Regular inspection and proper installation according to manufacturer guidelines are crucial for effective protection.
Fusible Plug Maintenance
Fusible plugs play a crucial role in maintaining the safety of high-temperature and high-pressure systems, such as compressed air and steam systems on marine vessels. Regular maintenance and inspection are essential to ensure that these plugs function properly when needed, preventing potential hazards like overheating, pressure buildup, or equipment failure.
Best Practices for Maintenance and Inspection
- Regular Inspections: Inspect fusible plugs regularly for signs of wear, corrosion, or physical damage. Look for cracks, discoloration, or any other indicators that the plug might fail to operate when needed. Ensure the plug is free from contaminants like oil or scale that could affect its function.
- Cleaning: Clean the surrounding areas of fusible plugs to remove any debris or contaminants that might interfere with their operation. For compressed air systems, ensuring that the air remains clean and free of oil or moisture is vital to prevent the plug from becoming coated or corroded.
- Testing: Follow the manufacturer’s guidelines for safe testing procedures to confirm that the fusible plug will function correctly under high temperatures. Some systems may have built-in testing features.
- Replacement: Periodically replace fusible plugs as part of a preventative maintenance strategy, and to comply with safety regulations or legislative requirements.
Compressed Air Systems Maintenance
Compressed air systems are generally maintained in a clean state to ensure the fusible plug remains in good condition. However, oil and moisture carryover from the compressors can potentially affect the plug’s functionality.
- Oil-Free Compressors: To prevent oil contamination, it is recommended to use oil-free compressors or install filters that can remove oil. Oil contamination can cause the fusible plug to become coated, affecting its ability to respond to high temperatures.
- Moisture Management: Moisture carry-over can also corrode or damage fusible plugs over time. To prevent this, desiccant or refrigeration dryers should be used to remove moisture from the compressed air system.
By maintaining a clean system and addressing oil and moisture issues, the fusible plug can be kept in optimal working condition. However, periodic replacement is necessary as part of a comprehensive preventative maintenance plan to ensure safety and compliance with industry regulations.
Steam Systems Maintenance
In steam systems, fusible plugs are exposed to a range of challenges that can impact their performance, particularly insulation that may form on the plug.
- Insulation Build-Up: On the water side of the plug, dissolved solids can solidify on heat transfer surfaces, forming scale. This scale acts as an insulating barrier, reducing the heat transfer rate of the boiler tubes and preventing the fusible plug from detecting the temperature correctly.
- Fire Side Insulation: On the fire side, soot or debris may accumulate, creating a similar insulating effect, which can cause the fusible plug to malfunction.
To maintain fusible plug effectiveness in steam systems, regular cleaning and de-scaling are essential to ensure the plug is not insulated. Ensuring proper heat transfer in both the water and fire sides will allow the fusible plug to respond quickly when the temperature exceeds safe limits.
Replacement Guidelines and Regular Safety Checks
Fusible plugs should be inspected and replaced according to the manufacturer’s recommendations, or more frequently if the system operates in harsh conditions. It is essential to follow industry regulations and safety standards to ensure fusible plugs perform their protective role when needed. Regular safety checks are crucial for identifying potential issues like corrosion, scaling, or contamination, preventing system failure, and safeguarding crew and equipment from catastrophic damage.
Fusible Plugs FAQ
Q. Where is a fusible plug located?
A. Fusible plugs are usually found on the crown sheet of a combustion chamber, the rear tube sheet in Scotch marine boilers, or the front tube sheet in firebox boilers.
Q. Why are fusible plugs used?
A. Fusible plugs are used to protect equipment from overheating, melting at high temperatures to release pressure and prevent accidents.
Q. Can a plug function without a fuse?
A. No, without a fuse, the plug will not work, as it relies on the fuse to manage power safely.
Q. What temperature does a fusible plug melt at?
A. Fusible plugs typically melt at temperatures around 100–110 °C (212–230 °F).
Conclusion
Fusible plugs are vital safety components in high-temperature and high-pressure systems, especially in marine applications where reliability and safety are paramount. By melting at a specific temperature, these simple yet effective devices protect against potentially catastrophic failures, ensuring the safety of equipment and personnel alike. Regular maintenance, correct installation, and understanding the specific requirements for different systems—such as compressed air and steam—are all essential for keeping fusible plugs in optimal working order.
As marine safety standards evolve, staying informed about best practices for fusible plug selection, installation, and upkeep is more important than ever. By following the latest guidelines, operators can ensure their vessels meet 2025’s updated safety requirements, providing peace of mind and a safer environment at sea.