Questions And Answers For Marine Engineers
The purpose of a list of Questions And Answers For Marine Engineers is to provide guidance and preparation for individuals looking to be hired as marine engineers. The list of questions and answers covers various topics related to marine engineering, such as technical knowledge, industry experience, problem-solving skills, and personal characteristics, among others. By preparing answers to these common questions, individuals can demonstrate their competency, confidence, and fit for the role of a marine engineer.
Q1: What is the purpose of O-rings in a centrifugal pump?
Answer:
O-rings in a centrifugal pump serve as static seals between stationary components, such as the pump casing and its cover, to prevent fluid or gas leakage. These seals are crucial in rotary equipment like pumps to stop the flow of liquids or gases from high-pressure areas to low-pressure regions. Over time, O-rings can degrade due to wear, abrasion, or environmental factors, requiring periodic replacement to maintain proper sealing and pump efficiency.
Q2: What is the priming procedure for a centrifugal pump?
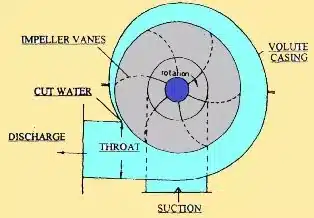
Answer:
Priming a centrifugal pump ensures the pump casing is filled with liquid, allowing it to operate efficiently. The priming steps are as follows:
- Fill the Suction Pipe: Ensure the suction pipe is filled with liquid and close the discharge valve.
- Open the Vent Valve: Open the vent valve on the pump casing to release trapped air.
- Fill the Pump Casing: Gradually pour liquid into the pump casing until it reaches the required level.
- Close the Vent Valve: Once the air has escaped and the pump is full, close the vent valve.
- Open the Discharge Valve: Open the discharge valve to allow liquid flow.
- Start the Pump: Switch on the pump and monitor the discharge pressure to verify proper priming and operation.
- Monitor Performance: Continuously observe the discharge pressure and adjust the flow rate as necessary to ensure optimal performance.
Note: Failure to properly prime the pump can lead to issues such as air binding, which impedes the pump’s functionality and efficiency.
Q3: What is the difference between a Globe Valve and a Gate Valve?
Answer:
The key differences between a globe valve and a gate valve are in their design, function, and pressure characteristics:
- Design and Structure:
- Globe Valve: Features a spherical body with a movable disk that regulates flow. The flow path is typically S-shaped, requiring the fluid to change direction, which results in a higher pressure drop.
- Gate Valve: Features a wedge-shaped or flat gate that opens or closes the flow route by moving vertically. It permits straight-line flow with little pressure loss or resistance when fully open.Function and Use:
- Globe Valve: Best for throttling and flow regulation, making it ideal for applications that require precise control over the flow rate.
- Gate Valve: Used for on/off control where full flow or complete shut-off is needed. It is not suitable for throttling as partial opening can cause damage.
- Pressure Drop:
- Globe Valve: Causes a significant pressure drop due to its flow path design.
- Gate Valve: Has minimal pressure drop when fully open, allowing efficient flow.
Q4: How can you identify 2-stroke and 4-stroke marine engines without opening them?
Answer:
You can distinguish between 2-stroke and 4-stroke marine engines by:
- Sound:
- A 2-stroke engine produces a louder, more rhythmic sound due to firing every revolution of the crankshaft.
- A 4-stroke engine has a smoother and less frequent sound, as it fires once every two revolutions.
- Exhaust:
- 2-stroke engines generally emit more visible exhaust because of the mixing of oil and fuel during operation.
- 4-stroke engines have cleaner exhaust as oil is not burned with the fuel.
- RPM and Power:
- 2-stroke engines typically operate at higher RPMs and have more power relative to their size.
- 4-stroke engines are built for efficiency and offer more reliable power.
Q5: What is the power transmission method from a marine generator to the Main Switchboard (MSB)?
Answer:
In marine systems, power transmission from the generator to the MSB is facilitated through busbars or electrical cables. These components are equipped with preferential trips and overload protection mechanisms to ensure safe and efficient power delivery. The electrical power generated by the generator is transmitted to the MSB, where it is distributed to various systems and loads onboard the vessel. This setup ensures the reliable and effective utilization of electrical power by the ship’s equipment and systems.
Q6: Why is wear in main bearings critical to the crankshaft and propeller shaft system on ships?
Answer:
Wear in the main bearings is critical because it can lead to shaft misalignment and excessive looseness in the crankshaft and propeller shaft system. Misalignment causes increased vibrations and accelerates wear on both the shafts and bearings, compromising their efficiency and lifespan. In severe cases, it can result in shaft failure, leading to significant damage to the propulsion system and posing safety risks to the crew and passengers. Regular maintenance and monitoring are crucial to preventing such issues and ensuring the smooth operation of the propulsion system.
Q7: What is the significance of large fillets in crankpins and journals?
Answer:
Large fillets around oil holes in crankpins and journals are crucial for several reasons:
- Prevention of Stress Concentration:
Large fillets evenly distribute stress across the surface, reducing the risk of stress concentration and cracking, especially at the corners of oil holes. - Improved Lubrication:
They enhance oil flow to the bearing surfaces, ensuring better lubrication and minimizing wear. - Increased Structural Strength:
Fillets add to the overall strength of crankpins and journals, making them more resistant to mechanical failure under load.
Q8: What are the causes and effects of torsional vibrations in a crankshaft?
Answer:
Causes:
Torsional vibrations in a crankshaft arise from:
- Imbalances in Rotating Mass: Uneven distribution of mass causes oscillations.
- Elasticity Variations: Differences in the shaft’s and its components’ elasticity.
- Combustion Forces: Fluctuating forces generated during engine operation.
Effects:
- Noise and Vibrations: Can range from minor disturbances to significant operational issues.
- Component Damage: Excessive vibrations may damage bearings, connecting rods, and the cylinder block.
- Fatigue and Failure: Long-term exposure can lead to crankshaft fatigue, eventual failure, and costly engine repairs.
Q9: What is critical speed, and what are its adverse effects on ships?
Answer:
Critical speed is the speed at which the natural frequency of a ship’s hull and superstructure aligns with the excitation frequency of external forces, such as sea waves. At this speed, the ship becomes highly susceptible to excessive vibrations, which can lead to:
- Structural Damage: Fatigue and weakening of the ship’s hull and superstructure.
- Reduced Stability: Increased risk of capsizing.
- Operational Issues: Discomfort for passengers and crew, damage to onboard equipment, and decreased overall efficiency.
Avoiding operation at or near critical speed is essential to maintain safety and performance.
Q10: What are fatigue cracks, and what crankshaft operating factors influence their occurrence?
Answer:
Fatigue cracks are structural failures caused by repeated cycles of loading and unloading, leading to material degradation over time. Several operating factors influence the likelihood of fatigue cracks in a crankshaft:
- Load Magnitude: Higher loads increase the stress on the crankshaft, accelerating crack formation.
- Load Frequency: Frequent loading cycles amplify the risk of fatigue.
- Stress Concentration: Sharp edges, notches, or imperfections create points of higher stress, making cracks more likely.
- Material Properties: Low-quality materials or improper heat treatment reduce resistance to fatigue.
Q11: How does a detuner or torsional vibration damper reduce the effects of torsional vibration?
Answer:
A torsional vibration damper, or detuner, minimizes torsional vibrations by introducing mechanical impedance to the system. The damper uses materials like rubber or fluid to absorb vibration energy and convert it into heat. By adding mass or damping elements to the rotating system, it alters the natural frequency of the torsional vibration system, moving it away from the excitation frequency. This reduces the amplitude of vibrations, preventing resonant amplification, enhancing the lifespan of machinery, and improving overall performance.
Q12: How can you identify fatigue failure?
Answer:
Fatigue failure results from repeated loading and unloading of material and can be identified by specific characteristics. Small cracks initially form on the material’s surface due to repeated stress. Over time, these cracks grow as loading continues, eventually leading to complete fracture. A fatigue fracture typically exhibits a distinct surface appearance, with a smooth region where the crack grew gradually and a rough region where sudden fracture occurred.
Q13: How is a fatigue crack initiated?
Answer:
A fatigue crack begins due to repeated cyclic loading on a material, which causes microscopic cracks to form and grow over time. These cracks typically start at the material’s surface and extend inward as loading continues, eventually resulting in failure. Factors affecting fatigue crack initiation include the material’s properties (such as grain structure and composition), loading conditions (such as stress amplitude and frequency), and the presence of defects or inclusions in the material.
Q14: What events lead to a main engine crankcase explosion?
Answer:
A crankcase explosion occurs in two key stages. The first event is the creation of an explosive mixture inside the crankcase. This happens when a “hot spot” heats the lubricating oil, causing it to vaporize. The vaporized oil rises and condenses on cooler parts of the crankcase, forming a white mist that falls within the explosion range and becomes flammable.
The second event involves the ignition of this oil mist, typically caused by the same or another hot spot. The resulting combustion leads to a rapid pressure rise, triggering an explosion within the crankcase.
Q15: What is a mist detector in a marine engine?
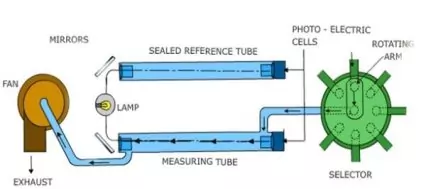
Answer:
A mist detector continuously monitors the concentration of oil mist in the crankcase. If the mist concentration rises above a predefined threshold due to overheating of bearings, the detector triggers an alarm and displays the mist level, alerting the crew to potential issues.
Q16: How can engine overheating be detected without using mist detectors?
Answer:
Engine overheating can be identified through various other indicators:
- Temperature Gauges: Rising coolant temperature shown on engine gauges indicates overheating.
- Warning Lights: Modern systems often have a dashboard warning light that illuminates when overheating occurs.
- Engine Performance: A noticeable drop in engine power or acceleration may signify overheating.
- Unusual Sounds: Knocking or ticking sounds from the engine can suggest overheating.
- Smoke: Excessive white smoke from the engine is often a sign of overheating.
Q17: How can the severity of a crankcase explosion be limited?
Answer:
A rapid increase in pressure within the crankcase can cause an explosion, leading to significant structural damage and the spread of flames throughout the engine compartment, which can result in personal injury. To control this pressure rise, a relief valve is installed in the crankcase. This valve opens when the pressure exceeds 0.02-0.1 bar, preventing over-pressurization of the engine structure. Additionally, the relief valve door is designed to close swiftly after opening, preventing the influx of fresh air into the crankcase where hot combustion gases may be present, thus reducing the risk of further ignition.
Q18: What is the procedure if crankcase overheating is indicated?
Answer:
In the event of crankcase overheating, immediate action is crucial to ensure the safety of engine room personnel and to prevent an explosion. Follow these steps:
- Evacuate the Crankcase: Leave the crankcase area immediately.
- Slow the Engine: Reduce engine speed and instruct the bridge to stop the engine.
- Stop the Fuel Supply: Once the engine has stopped, cut off the fuel supply.
- Shut Off the Auxiliary Fan: Turn off the auxiliary fan to limit airflow.
- Ventilate the Engine Room: Open skylights and storage hatches to allow air circulation.
- Exit the Engine Room: Leave the engine room immediately.
- Secure the Area: Lock the engine room entrance and prevent unauthorized access.
- Prepare for Firefighting: Ensure firefighting equipment is ready for use.
- Wait Before Opening the Crankcase: Do not open the crankcase for at least 20 minutes after the engine has stopped, and ensure the oil mist detector or bearing temperature monitor alarm is reset.
- Stop the Lubricating Oil Circulation Pump: Turn off the lubricating oil circulation pump.
- Close the Starting Air: Shut the starting air valve and activate the rotary gearbox.
- Identify Hot Spots: Locate the cause of the overheating (such as overheating oil).
- Perform a Permanent Fix: Address and correct the underlying issue causing the overheating.
Q19: What are the issues associated with effectively lubricating liner and piston assemblies in large slow-speed engines?
Answer:
Lubricating the liner and piston assemblies in large slow-speed engines presents several challenges, including:
- Contamination: Dirt, debris, and other contaminants can mix with the lubricant, leading to wear and damage to engine components.
- Temperature: The high operating temperatures at critical points, like top dead center, can degrade the lubricant, reducing its effectiveness and causing increased wear on components.
- Pressure: The high pressures within the engine can force the lubricant out of critical areas, leading to insufficient lubrication and accelerated wear.
- Cavitation: The rapid motion of the pistons and liners can create cavitation—vapor pockets in the lubricant. These pockets collapse, causing damage to the components and reducing lubrication effectiveness.
- Compatibility: The lubricant must be compatible with the engine components, the fuel being used, and the operating environment. Any mismatch can lead to inadequate lubrication or engine damage.
- Lubricant Consumption: Large slow-speed engines consume large amounts of lubricant, which can be a significant cost burden for ship owners.
- Oil Distribution: Oil is injected at specific points in the engine, which can lead to an oversupply at certain locations and undersupply at others, disrupting effective lubrication.
- Residual Fuels: The use of residual fuels, which often contain acids and abrasives, can reduce the effectiveness of the lubricant, accelerating wear and corrosion of engine parts.
- Inconsistent Lubricant Supply: The oil supply rate is typically controlled by engine speed, which can result in a mismatch with the actual lubrication requirements across a wide operating range. At low loads or during load changes, this can lead to insufficient lubrication.
- Hydraulic Pressure: At top dead center, the hydraulic pressure that builds between the piston ring and liner collapses, which can cause a reduction in lubrication effectiveness, especially at high temperatures.
- Lubrication Effectiveness: The combination of high temperatures, pressure fluctuations, and rapid piston motion can compromise the ability of the lubricant to fully protect the liner and piston assemblies, leading to increased wear and the potential for engine failure.
Q20: What investigations and corrective actions are required if the engine does not start on air?
Answer:
If the engine fails to start on air, follow these steps to investigate and take corrective actions:
- Check Air Pressure in the Starting Air Vessel: Ensure there is adequate air pressure in the starting air vessel. If the air tank valve is closed, open it.
- Inspect Air Pressure in the Engine Manifold: Low air pressure in the engine manifold could indicate an issue with the air compressor, such as malfunction or excessive air consumption. Verify that all air compressors are functioning correctly, and that air consumption is limited to engine operation.
- Visual Inspection of Turning Gear and Interlock Switch: Check the position of the turning gear and the interlock switch. If the turning gear is engaged, disengage it to allow the engine to start.
Blog Conclusion
In conclusion, this blog highlights some of the most frequently asked questions and answers in a marine engineer interview. As a marine engineer, it’s crucial to have a strong understanding of ship machinery, hands-on experience, and the ability to effectively communicate your skills and expertise. Preparing for the interview by practicing responses to these common questions can significantly improve your chances of securing the role. Focus on showcasing your strengths, emphasizing your relevant experience, and demonstrating your enthusiasm for the maritime industry. Best of luck!